Bien plus que de simples consommables de fabrication, les conditionnements thermoformés utilisés chez les équipementiers automobiles jouent un rôle clé dans la performance des lignes de production et tout au long de la supply chain. Alors que vous soyez chargé du suivi de production, des projets d’industrialisation, de l’amélioration continue ou de la logistique, découvrez pourquoi le sujet des conditionnements est si déterminant pour votre productivité.
Le rôle élargi du conditionnement thermoformé
Pour les non-avertis, les conditionnements thermoformés sur ligne peuvent sembler jouer un rôle secondaire dans le processus de fabrication. Mais il n’en est rien, les packagings thermoformés sont en effet indispensables à la production et font partie intégrante de l’outil de production puisqu’ils sont utilisés tout au long du process. Leur rôle est en effet bien plus large que ce que l’on peut imaginer car ils permettent :
- l’approvisionnement des machines en composants,
- le bon déroulement des différentes opérations de production automatisées,
- la manutention des pièces par les opérateurs,
- la protection face aux chocs et aux décharges électrostatiques,
- le transport entre les différents sites
Pour illustrer leur importance, chez les équipementiers automobiles internationaux, les pièces peuvent en effet passer par différents sites de fabrication aux quatre coins du monde, subir plusieurs manipulations par les opérateurs ou par les machines de production tout au long du process … Les conditionnements thermoformés sont alors le trait d’union entre toutes ces étapes et circulent entre les différents sites.
Des produits techniques, mais pas seulement
Les conditionnements industriels sont des produits techniques réalisés par des spécialistes de la plasturgie. Ces produits prennent le plus souvent la forme de plateaux, de blisters ou d’alvéoles. En fonction de l’application plusieurs paramètres influent sur leur design et leur technicité :
- le type de pièce à contenir : pièce mécanique, composants électroniques…
- le mode de manipulation : manuel par un opérateur ou automatique par robot ou machine spéciale
- la forme de la pièce et la position de son centre de gravité
- l’état de surface et l'importance de protéger l’esthétique
- la mobilité de la pièce à l’intérieur du conditionnement
Bien spécifier et bien concevoir les conditionnements sur ligne est donc très important, car des packagings inadaptés peuvent générer divers problèmes comme des casses de pièce, des imprécisions d’assemblage, des pièces mal saisies par les robots, des rayures ou des chocs … Autant de problèmes qui peuvent impacter la productivité des équipements.
Cette étape de spécification technique des conditionnements est le plus souvent bien maitrisée par les industriels et leurs fournisseurs. Mais la partie souvent moins abordée jusque-là est celle qui concerne la boucle logistique et le bon dimensionnement des volumes de conditionnements nécessaires pour ne jamais être à court et faire face à toutes les situations.
Éviter les arrêts de production en disposant des bons conditionnements aux bons endroits
En effet, comme précisé plus haut, les plateaux de conditionnement peuvent circuler entre plusieurs sites : les différentes usines internes à l’entreprise, les sites des sous-traitants et les sites du client.
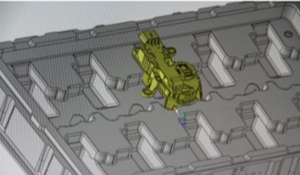
Souvent chez les grands équipementiers, une fois la production série lancée, les conditionnements peuvent alors se retrouver dispersés aux 4 coins de la France ou du monde et cela peut vite devenir problématique si les volumes de conditionnement ne sont pas adaptés. En effet, à cause de différents événements, les packagings peuvent venir à manquer et stopper net une ligne de production.
Le plus souvent, les problèmes de conditionnements viennent :
- d’une définition trop juste des quantités nécessaires lors de la phase P1 du projet et d’un déficit de conditionnements à l’étape P0 pour suivre la montée en charge
- d’une boucle de retour des conditionnements mal optimisée où qui change avec le temps sans être réévaluée (nouveaux sous-traitants, nouvelle étape de stockage)
- d’événements inattendus qui bloquent une partie des conditionnements dans les différents sites (arrêts de production, problèmes transporteurs…)
- d’un manque de suivi sur les quantités nécessaires au fil du temps pour absorber la production (montée en charge, pic de production, …) et la perte de conditionnement (usure, casse,...) qui fait que l’on découvre le problème trop tard
Avoir les bons conditionnements est donc indispensable, mais en avoir suffisamment l’est tout autant au risque de voir sa production arrêtée et son taux de service client dégradé.
💡Les arrêts de vos lignes robotisées sont-ils liés à la planéité de vos plateaux thermoformés ?
Note : S’il existe bien des packagings de substitution dans certains cas, ceux-ci n’ont qu’un rôle de secours. En effet, lorsqu’ils existent, ces conditionnements de substitution n’ont été imaginés que pour des cas d’urgence et ponctuels. Ils sont en principe plus fins, non-réutilisables et ne peuvent donc pas être utilisés comme solution “dégradée” dans la durée... |
Étudier correctement la boucle logistique en phase P1 du projet et la suivre avec précision en phase P0
Pour conclure, il est impératif de bien définir les volumes de conditionnement en phase projet pour pouvoir produire plus sereinement en phase série. Bien sûr, le but n’est pas de surdimensionner, mais de prévoir au plus juste en analysant toutes les étapes de production, les durées d’opération, les temps de stockage, les temps de transport afin d’identifier toutes les sources de pénuries et de blocage possibles. Ce travail doit aussi être repris dans la durée pour faire face aux changements qui peuvent impacter cette boucle logistique : un nouveau site de production, un contrôle supplémentaire à effectuer chez un sous-traitant, une augmentation de la production à venir...
Ainsi, au-delà de son expertise technique sur le thermoformage de plateaux industriels, l’entreprise Bourgeois Plastique accompagne plus largement ses clients pour prendre la problématique dans son ensemble. L’entreprise a notamment mis au point une méthodologie simple et inédite pour accompagner les sites clients dans la définition de leurs besoins techniques et logistiques relatifs aux conditionnements industriels.